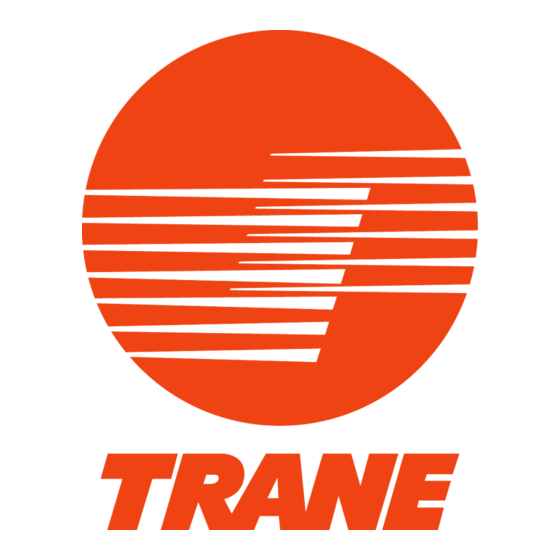
- Trane Manuals
- Air Conditioner
- Voyager Commercial
- Installation & operation manual

Trane Voyager Commercial Installation & Operation Manual
- Manual (93 pages)
- Installation, operation and maintenance manual (156 pages)
- page of 152 Go / 152
Table of Contents
- Literature Change History
- Overview of Manual
- 60 Hz Description
Model Number Descriptions
- 50 Hz Description
- Model Number Descriptions 50 Hz Description
General Information
- About the Unit
- Precautionary Measures
- First Aid Measures
- Unit Inspection
Pre-Installation
- Downflow Models Only
- Field Installed Control Wiring
- Gas Heat Requirements
Unit Dimensions and Weights
- Roof Curb and Ductwork
- Horizontal Ductwork
- Unit Dimensions and Weights Recommended Clearances
- Unit Rigging and Placement
Installation General Requirements
- Condensate Drain Connection
- O/A Sensor & Tubing Installation
- Units with Statitrac
Installation Electrical
- Disconnect Switch External Handle (Factory Mounted Option)
- Thru-The-Base Electrical (Optional Accessory)
- Low Voltage Wiring
- Control Power Transformer
- Field Installed AC Control Wiring
- Field Installed DC Control Wiring
- Constant Volume Control Options
- Variable Air Volume Control Options
- Remote Minimum Position Potentiometer
Installation Piping
- Connecting the Gas Supply Line to the Furnace Gas Train
- Unit Control Modules
- Microelectronic Control Features
- Variable Air Volume Applications
- Constant Volume or Variable Air Volume Applications
- Electrical Phasing
- Voltage Supply and Voltage Imbalance
- Verifying Proper Fan Rotation
- Verifying Proper Air Flow (CFM)
- Exhaust Fan Operation
- Economizer (O/A) Dampers
- Manual Fresh Air Damper
- Starting 27.5 to 35 Ton Units
- Starting 40 to 50 Ton Units
- Compressor Oil
- Scroll Compressor Operational Noises
- Compressor Crankcase Heaters
- Charging by Subcooling
- Measuring Subcooling
- Gas Heat Units
- Electric Heat Units
- For Constant Volume Units
- For Variable Air Volume Units
Sequence of Operation
- Mechanical Cooling Sequence of Operation
- Units Without an Economizer
- Economizer Operation Based on Dry Bulb
- Economizer Operation Based on Reference Enthalpy
- Economizer Operation Based on Comparative Enthalpy
- Gas Heat Sequence of Operation
- Electric Heat Sequence of Operation
- Low Pressure Control (LPC) Sequence of Operation (Reliatel Control)
- High Pressure Control and Temperature Discharge Limit (Reliatel Control)
Maintenance
- Fan Belt Adjustment
- Monthly Maintenance
- Cooling Season
- Heating Season
- Coil Cleaning
- Fall Restraint
- Refrigerant Evacuation and Charging
- Precision Suction Restrictor
Diagnostics
- Terminal Locations
- Diagnostics (CV Units Only)
- Diagnostics (VAV Only)
- Resetting Cooling and Ignition Lockouts
- Zone Temperature Sensor (ZSM) Service Indicator
- RTRM Zone Sensor Module (ZSM) Test
- Programmable & Digital Zone Sensor Test
- Reliatel Refrigeration Module (RTRM)
- Reliatel Air Module (RTAM) Test
- Compressor-Blink Codes
- TR-1 and TR-200 VFD Programming Parameters
Unit Wiring Diagram Numbers
Warranty and liability clause.
- Commercial Equipment Rated 20 Tons and Larger and Related Accessories
Advertisement
Quick Links
- 1 Model Number Descriptions
- 2 60 Hz Description
- 3 Unit Wiring Diagram Numbers
- Download this manual
Related Manuals for Trane Voyager Commercial

Summary of Contents for Trane Voyager Commercial
- Page 1 Installation, Operation, Maintenance Voyager™ Commercial 27.5 to 50 Ton 60 Hz 22.9 to 41.7 Ton 50 Hz CV or VAV Rooftop Air Conditioners with ReliaTel™ Controls, R-410A Refrigerant Model Numbers “B” and later design sequence TC*, TE*, YC*330B, 360B, 420B, 480B, 600B (60 Hz/3 phase) TC*, TE*, YC*275B, 305B, 350B, 400B, 500B (50 Hz/3 phase) SAFETY WARNING Only qualified personnel should install and service the equipment.
Page 2: Literature Change History
Page 3: overview of manual, page 4: table of contents.
- Page 5 Constant Volume Control Options ....... 41 Variable Air Volume Control Options ......43 Installation Piping .
- Page 6 Gas Heat Sequence Of Operation ........115 Electric Heat Sequence Of Operation .
- Page 7 TR-1 and TR-200 VFD Programming Parameters ....146 Unit Wiring Diagram Numbers ......... 148 Warranty and Liability Clause .
Page 8: 60 Hz Description
- Page 9 Model Number Descriptions Discharge Temperature Sensor Clogged Filter Switch Digit 32 — Dehumidification Option Modulating Hot Gas Reheat Model Number Notes All voltages are across the line starting only. 2. Option includes Liquid, Discharge, Suction Valves. 3. Supply air fan drives A thru G are used with 27½-35 ton units only and drives H thru N are used with 40 &...
Page 10: 50 Hz Description
Page 11: general information, page 12: about the unit, page 13: first aid measures, page 14: pre-installation, page 15: field installed control wiring, page 16: unit dimensions and weights.
- Page 17 Unit Dimensions and Weights Figure 1. 60 Hz 27½-35, 50 Hz 23-29 Tons (TC, TE, YC Low Heat) Figure 2. Rear view showing duct openings for horizontal units 1 1/4 3 1/4 (32) (81) RT-SVX34C-EN...
- Page 18 Unit Dimensions and Weights Figure 3. 60 Hz 27½-35, 50 Hz 23-29 Tons (TC, TE, YC Low Heat) NOTES: 1. SEE DETAIL HOOD DRAWING FOR HORIZONTAL / DOWNFLOW UNITS FOR ADDITIONAL DIMENSION AND LOCATION. 90 3/8" 2295.5mm 180 5/16" 4579.9mm SEE NOTE 2 3.25 [82.55mm] TO TOP OF FAN GRILLE 70 7/16"...
- Page 19 Unit Dimensions and Weights Figure 5. Duct openings, 60 Hz 27½-35, 50 Hz 23-29 Tons (YC High Heat) 1 1/4 3 1/4 (32) (81) Figure 6. 60 Hz 27½-35, 50 Hz 23-29 Tons (YC High Heat) 90 5/8" NOTES: 2301.8mm 1.
- Page 20 Unit Dimensions and Weights Figure 7. 60 Hz 40-50, 50 Hz 33-42 Tons (TC, TE, YC Low and High Heat) Figure 8. Duct openings, 60 Hz 40-50, 50 Hz 33-42 Tons (TC, TE, YC Low and High Heat) 1 1/4 3 1/4 (32) (81)
- Page 21 Unit Dimensions and Weights Figure 9. 60 Hz 40-50, 50 Hz 33-42 Tons (TC, TE, YC Low and High Heat) NOTES: 90 5/8" 1. SEE ROOFCURB DRAWING FOR DETAILS 2301.8mm ON FIELD DUCT FITUP AND CONNECTIONS 2. SEE DETAIL HOOD DRAWING FOR HORIZONTAL / DOWNFLOW UNITS FOR ADDITIONAL DIMENSION AND LOCATION.
Page 22: Unit Rigging And Placement
- Page 23 Unit Dimensions and Weights Figure 12. Unit Rigging Table 1. Minimum Operating Clearances Installation (Horizontal and Downflow Configurations) Recommended Clearances Economizer/ Condenser Coil Single Unit Exhaust End Orientation End/Side Service Side Access TC*, TE*, YC* 6 Feet 8 Feet 4 Feet 27.5 to 50 Tons Distance Between Units Economizer/...
- Page 24 Unit Dimensions and Weights Figure 13. Center of Gravity Z (see note 2) Table 3. Center of Gravity Center-of-Gravity (inches) YC Low Heat YC High Heat Unit Model Dimension Dimension TC/TE Dimension ***330/275* ***360/305* ***420/350* ***480/400* ***600/500* Note: Center-of-gravity dimensions are approximate, and are based on the unit equipped with: standard efficiency coils, standard efficiency motors, economizer, inlet guide vanes, and throwaway filters Note: Z dimension is upward from the base of the unit.
- Page 25 Unit Dimensions and Weights Table 5. Point Loading Average Weight1 — lbs./kg Model **D330/275 **H330/275 **D360/305 **H360/305 **D420/350 **H420/350 **D480/400 **H480/400 **D600/500 **H600/500 Notes: 1. Point Loading is identified with corner A being the corner with the compressors. As you move clockwise around the unit as viewed from the top, mid-point B, corner C, corner D, mid-point E and corner F.
Page 26: Installation General Requirements
Page 27: units with statitrac.
- Page 28 Installation General Requirements Figure 16. Statitrac Transducer Assembly Static Reference Tubing Connects Here (O/A Sensor) Space Pressure Sensing Tube Space Pressure Connects Here Transducer Space Pressure Calibration Solenoid Space Pressure Transducer Sensing Tube to Space LO HI Pressure Sensing Tube to Outside Air Reference RT-SVX34C-EN...
Page 29: Installation Electrical
Page 30: main power wiring.
- Page 31 Installation Electrical Figure 18. Typical Field Power Wiring RT-SVX34C-EN...
- Page 32 Installation Electrical Table 7. 27½-50 Ton Electrical Service Sizing Data—60Hz1 Fan Motors Compressor Supply Condenser Exhaust Allowable Electrical Voltage 100% Model Characteristics Range No/Ton (Ea.) (Ea.) No HP (Ea.) 50% (Ea.) 21.5 1/12,1/ 208/60/3 187-229 44.0/50.5 304/315 10.0 29.0 1/12,1/ 18.8 230/60/3 207-253...
- Page 33 Installation Electrical Table 7. 27½-50 Ton Electrical Service Sizing Data—60Hz1 Fan Motors Compressor Supply Condenser Exhaust Allowable Electrical Voltage 100% Model Characteristics Range No/Ton (Ea.) (Ea.) No HP (Ea.) 50% (Ea.) 10.0 29.0 2/13,1/ 208/60/3 187-229 50.5/56.0 315/351 15.0 40.7 20.0 56.1 10.0...
- Page 34 Installation Electrical Table 9. Electrical Service Sizing Data—50Hz Fan Motors Compressor Supply Condenser Exhaust 100% Electrical Characteristic Model No/Ton (Ea.) (Ea.) HP(kW) FLA No. HP(kW) (Ea.) (kW) (Ea.) 13.6/ TC/TE/YC*275 380-415/50/3 1/10, 1/11 21.0/23.0 147/ 158 7.5 (5.6) .75 (.56) 14.1 (.56) 16.0/...
Page 35: Electrical Wire Sizing And Protection Device Equations
Page 36: low voltage wiring, page 37: control power transformer, page 38: field installed dc control wiring.
- Page 39 Installation Electrical Figure 19. Typical Field Wiring Requirements for CV Control Options LTB6 Space Humidity Sensor Space Humidistat RT-SVX34C-EN...
- Page 40 Installation Electrical Figure 20. Typical Field Wiring Requirements for VAV Control Options LTB6 Customer Changeover for VAV Htg (MOD GAS ONLY *VAV Mode input: RTRM J6-2 to RTRM J6-4 If the unit does not have a Mode (Off, Auto) input from another source, the following default applies: Short from J6-2 to J6-4 = AUTO mode, Open from J6-2 to J6-4 = OFF mode.
Page 41: Remote Panels And Sensors
- Page 42 Installation Electrical Figure 22. Zone Panel (BAYSENS106*) SINGLE SETPOINT MANUAL CHANGE OVER Zone Panel (BAYSENS108*) This electronic sensor features four system switch settings (Heat, Cool, Auto, and Off) and two fan settings (On and Auto). It is a manual or auto changeover control with dual setpoint capability. It can be used with a remote zone temperature sensor BAYSENS077*.
Page 43: Variable Air Volume Control Options
- Page 44 Installation Electrical Table 14. Variable Air Volume Mode Operation System Mode Fan "Auto "Fan "On" DWU Active Heat DWU Off VAV Heating Cool VAV Cooling VAV Cooling 1,2,3,4 1,2,3,4 DWU Active DWU or Cooling DWU or Cooling Auto DWU Off VAV Cooling VAV Cooling or Heating Notes:...
- Page 45 Figure 27. Remote Zone Sensor (BAYSENS073*) Remote Zone Sensor (BAYSENS074*) This electronic sensor features single setpoint capability and timed override with override cancellation. It is used with a Trane Integrated Comfort building management system. Figure 28. Remote Zone Sensor (BAYSENS074*) Remote Zone Sensor (BAYSENS077*) This electronic sensor can be used with BAYSENS106*, 108*, 110*, 119*, or 021* Remote Panels.
- Page 46 Installation Electrical The liquid crystal display (LCD) displays zone temperature, temperature setpoints, week day, time, and operational mode symbols. The options menu is used to enable or disable these applicable functions: Morning warm-up, economizer minimum position override during unoccupied status, heat installed, remote zone temperature sensor, 12/24 hour time display, and daytime warm-up.
Page 47: Remote Minimum Position Potentiometer
- Page 48 Installation Electrical Figure 32. Space Temperature Averaging To RTRM J6-1 and J6-2 or to ZSM terminals 1 and 2 or NSB panel terminals S1 and S2. Shield to terminal 11. Table 15. Temperature vs. Resistance (temperature vs. resistance coefficient is negative) Nominal Degrees F°...
- Page 49 Installation Electrical Table 15. Temperature vs. Resistance (temperature vs. resistance coefficient is negative) Nominal Degrees F° Resistance 50° 19.96 K - Ohms 55° 17.47 K - Ohms 60° 15.33 K - Ohms 65° 13.49 K - Ohms 70° 11.89 K - Ohms 75°...
Page 50: Installation Piping
Page 51: connecting the gas supply line to the furnace gas train.
- Page 52 Installation Piping Table 17. Specific Gravity Multiplier Specific Gravity Multiplier 0.55 1.04 0.65 0.96 Figure 33. Gas Train Configuration for Low Heat Units (high heat units utilize two gas trains.) RT-SVX34C-EN...
Page 53: Startup
- Page 54 Startup Figure 34. RTAM Module = Supply Air Heating Setpoint 2 = Static Pressure Setpoint (iwc) 3 = Static Pressure Deadband (iwc) 4 = Reset Setpoint 5 = Reset Amount 6 = Morning W armup Setpoint 7 = Supply Air Cooling Setpoint RTAM Figure 35.
- Page 55 Startup Figure 36. RTVM Module = Space Pressure Deadband (iwc) = Space Pressure Deadband (iwc) 2 = Space Pressure Setpoint (iwc) = Space Pressure Deadband (iwc) 2 = Space Pressure Setpoint (iwc) 2 = Space Pressure Setpoint (iwc) = Space Pressure Deadband (iwc) 2 = Space Pressure Setpoint (iwc) RTVM RTVM...
- Page 56 This module is used when the application calls for a BACnet building management type control system. It allows the control and monitoring of the system through a Trane Tracer SC panel or 3rd party BACnet system. The module can be ordered from the factory or ordered as a kit to be field installed.
Page 57: System Operation
- Page 58 Startup 2. Delay between stages timer function. When combined with a standard Zone Sensor Module, the Reliatel Refrigeration Module (RTRM) provides a 10 second minimum “ON” delay for compressor staging. 3. Built in Fan Delay Relay function for Constant Volume Units. When the fan mode switch on the Zone Sensor Module is set in the auto position, the RTRM provides individual supply fan timing sequences for each system in heating and cooling.
- Page 59 Startup 1. The zone temperature minus the economizer setpoint, and 2. The zone temperature minus the outdoor air temperature. Note: Table 19 lists the percentages the dampers will open based on these conditions. Table 19. Percent of Damper Travel Zone Temp - Econ Setpoint °F Zone - ODT 0.0 - 0.5 0.5 - 1.0...
- Page 60 Startup Figure 39. Compressors Zone Temperature - Occupied Cooling (CV only) When the unit is in the cooling mode and the zone temperature raises above the cooling setpoint controlband, the economizer and the compressor stages will be cycled as required by the zone sensor, remote panel, or Tracer®.
Page 61: Variable Air Volume Applications
- Page 62 Startup Daytime Warm-up (DWU) Control Daytime Warm-up is applicable during occupied status and when the zone temperature is below the initiation temperature. It can be activated or deactivated through ICS or a night setback zone sensor. If ICS or a night setback zone sensor is not utilized, DWU can be activated by setting the DWU enable DIP switch (RTAM) to ON and supplying a valid morning warm-up setpoint.
Page 63: Constant Volume Or Variable Air Volume Applications
- Page 64 Startup Table 21. Economizer Effectiveness Method used to determine econmizer effectiveness Required Comparative Enthalpy OAT, OAH, RAT, RAH Reference Enthalpy OAT, OAH Reference Dry Bulb Unable to determine effectiveness OAT data is invalid or unavailable Two of the three methods for determining the suitability of the outside air can be selected utilizing the potentiometer on the Economizer Actuator, as described below: 1.
- Page 65 Startup can be set for a particular application. The clogged filter switch is normally open and will automatically close when the pressure differential across the filters falls below the clogged filter setpoint. The RTOM will generate a SERVICE diagnostic that will be sent to the zone sensor or remote panel when the clogged filter switch has been closed for at least 2 minutes during supply fan operation.
- Page 66 Startup Phase Monitor The Phase Monitor is a 3 phase line monitor module that protects against phase loss, phase reversal and phase unbalance. It is intended to protect compressors from reverse rotation. It has an operating input voltage range of 190-600 VAC, and LED indicators for ON and FAULT. There are no field adjustments and the module will automatically reset from a fault condition.
- Page 67 Startup Figure 41. Transducer Voltage Output vs. Pressure Input for Supply, Return and Building Pressure -0.75 to 9.0 Iwc Pressure Transducer Voltage Output vs. Pressure Input 4.50 4.00 3.50 3.00 2.50 2.00 1.50 1.00 0.50 0.00 Pressure (inches w.c.) Power Exhaust Control (Tracking) The power exhaust dampers proportionally track or follow the fresh air (economizer) damper position.
- Page 68 Startup Coil Frost Protection The Frostat™ control monitors the suction line temperature to prevent the evaporator from freezing due to low operating temperatures whenever there is a demand for cooling. When a closed circuit has occurred for 5 seconds minimum, the RTRM turns off all of the cooling outputs providing the 3 minute minimum "On"...
- Page 69 Startup Table 25. Condenser Fan/Compressor Sequence O/A Temp. Unit Size Compressor Staging Sequence Condenser Fan Output (°F) (Tons) Step 1 Step2 Step 3 Output A Output B Fans "Off" Fan #2 Fan #3, 4 CPR 1 ** Fan #2 Fan #3, 4 CPR 2*** Fan #2 CPR 1, 2...
Page 70: Preparing The Unit For Operation
Page 71: voltage supply and voltage imbalance, page 72: starting the unit.
- Page 73 Startup at a time, when a jumper is installed across the test terminals. The unit will start the first test step and change to the next step every 30 seconds. At the end of the test mode, control of the unit will automatically revert to the applied "System"...
- Page 74 Startup Table 28. Test Mode States for VAV Units with Modulating Dehumidification TEST Cool Reheat STEP MODE ECON COMP 1 COMP 2 HEAT 1 HEAT 2 Pumpout Valve Valve IGV TEST OPEN OPEN CLOSED 100% IGV TEST CLOSED CLOSED 100% CLOSED MIN VENT 100%...
Page 75: Verifying Proper Fan Rotation
- Page 76 Startup 2. To determine the actual CFM (within + 5%), plot the fan's operating RPM and the Theoretical BHP onto the appropriate Fan Performance Curve in Figure 43, p. 78 Figure 44, p. Theoretical BHP Formula: Actual Motor Amps ----------------------------- ------------------------------------------ - Motor HP Theoretical BHP Motor Nameplate Amps...
- Page 77 Startup Table 31. Supply Fan Performance—40 and 50 Ton—60 Hz Total Static Pressure (in. wg)1 0.25 0.50 0.75 1.00 1.25 1.50 1.75 2.00 2.25 CFM Std. RPM BHP RPM BHP RPM BHP RPM BHP RPM BHP RPM BHP RPM BHP RPM 12000 2.29 2.86...
- Page 78 Startup Figure 43. Supply Fan Performance Curves 27.5 - 35 Ton—60Hz Supply Fan Performance 27-35T 2000 4000 6000 8000 10000 12000 14000 16000 18000 20000 22000 24000 26000 Volumetric Airflow Rate(CFM) Figure 44. Supply Fan Performance Curves 40 and 50 Ton—60Hz Supply Fan Performance 40 and 50 Ton 2000 4000...
- Page 79 Startup — Table 32. Supply Fan Performance 22.9-29.1 Ton (I-P)—50 Hz Static Pressure (in. wg) 0.25 0.50 0.75 1.00 1.25 1.50 1.75 2.00 2.25 RPM BHP RPM BHP RPM BHP RPM BHP RPM BHP RPM BHP RPM BHP RPM BHP RPM BHP 6670 283 0.80 351 1.18...
- Page 80 Startup Figure 45. Supply Fan Performance—22.9-29.2 Tons—50Hz Supply Fan Performance (996) (872) (747) (623) (498) (374) (249) (125) (0.0) 2000 4000 6000 8000 10000 12000 14000 16000 18000 20000 22000 24000 26000 Volumetric Airflow Rate(CFM) (.94) (1.89) (2.83) (3.78) (4.72) (5.66) (6.61) (7.55)
- Page 81 Startup — Table 33. Supply Fan Performance 82-105 kW (SI)—50 Hz Static Pressure (Pascals) 62.9 124.1 186.2 248.3 310.4 372.5 434.6 496.7 558.8 (L/s) RPM (kW) RPM (kW) RPM (kW) RPM (kW) RPM (kW) RPM (kW) RPM (kW) RPM (kW) RPM (kW) 3148 0.59 0.88...
- Page 82 Startup — Table 34. Supply Fan Performance 33.3 and 41.7 Tons (I-P)—50 Hz Static Pressure (in. wg) 0.25 0.50 0.75 1.00 1.25 1.50 1.75 2.00 2.25 9996 1.46 1.95 2.49 3.04 3.64 4.25 4.92 5.59 6.23 10829 1.78 2.30 2.87 3.44 4.06 4.71...
- Page 83 Startup Figure 46. Supply Fan Performance—33.3 and 41.7 Ton (IP)—50Hz Supply Fan Performance 40 and 50 Ton (1245) (996) (747) (498) (249) (0.0) 2000 4000 6000 8000 10000 12000 14000 16000 18000 20000 22000 24000 26000 28000 Volumetric Airflow Rate(CFM) (.94) (1.89) (2.83)
- Page 84 Startup — Table 35. Supply Fan Performance 105-148 kW (SI)—50 Hz Static Pressure (Pascals) 62.1 124.2 186.3 248.1 310.4 372.5 434.6 496.7 558.8 (L/s) RPM (kW) RPM (kW) RPM (kW) RPM (kW) RPM (kW) RPM (kW) RPM (kW) RPM (kW) RPM (kW) 4717 1.09 1.46...
- Page 85 Startup Table 36. TC*/YC* 300 - 600 MBH Economizer (R/A) Damper Pressure Drop — 60 Hz Unit Airflow Pressure Unit Airflow Pressure Unit Airflow Pressure Capacity (Cfm) Drop Capacity (Cfm) Drop Capacity (Cfm) Drop 27.5 8000 0.035 9000 0.042 10000 0.051 8000 0.035...
- Page 86 Startup Table 37. Component Static Pressure Drops (in. W.G.)1—60 Hz Heating System Filters2 MERV1 Throw- 4 High Gas Heat Electric Heat3 ID Coil away MERV 8 High Eff. Inlet Nominal Guide Tons Std Air High Element Element 2" 2" 4" 4"...
- Page 87 Startup Table 38. Supply Fan Drive Selection — 60Hz 7.5 HP 10 HP 15 HP 20 HP Nominal Drive Drive Drive Drive Tons 750* 27.5T 790** 800* Notes: * For YC gas/electric only. ** For TC and TE Cooling and Electric Heat units only. RT-SVX34C-EN...
- Page 88 Startup Table 39. Component Static Pressure Drops in. wg (I-P)—50 Hz Heating System Filters Throw- MERV14 Gas Heat Electric Heat ID Coil away MERV 8 High Eff. High Eff Nominal Inlet Std Tons Guide (kW) Std Air High Element Element 2”...
- Page 89 Startup Table 40. Component Static Pressure Drops Pa (SI)—50 Hz Heating System Filters MERV1 Throw- MERV 8 High 4 High Gas Heat Electric Heat ID Coil away Eff. Nominal Inlet Std Tons Guide (kW) Std Air High Element Element Adder 50 mm Vanes Economizer 3150...

Page 90: Exhaust Fan Operation
- Page 91 Startup Verify that the fans are operating properly and the CFM is within the job specifications. Refer to power exhaust fan performance tables beginning with Table 42, p. 92 for the exhaust fan performance characteristics. Available power adjustments: 1. The power exhaust fan(s) comes on based on the position of the of the exhaust fan setpoint potentiometer on the RTOM (Reliatel Options Module).
- Page 92 Startup Table 42. Power Exhaust Fan Performance—27.5-35 Ton—60 Hz Power Exhaust Selection 50% (min) 100% (max) Damper Blade Open Distance (in) 1.5 (min) 4.0 (max) 1.5 (min) 4.0 (max) Return Duct Static (in. wc) 3812 6866 7624 13742 3497 5296 6995 10591 3190...
- Page 93 Startup Table 45. Power Exhaust Fan Performance—33.3 - 41.7 Ton—50 Hz Power Exhaust Selection 50% (min) 100% (max) Damper Blade Open Distance (mm) 38.1 (min) 101.6 (max) 38.1 (min) 101.6 (max) Return Duct Static (Pa) 1909 3160 3818 6321 24.9 1800 2915 3599...
Page 94: Economizer Damper Adjustment
- Page 95 Startup 3. Add the measured return duct static pressure and the return air damper pressure drop together to obtain the Total Return Static Pressure. Apply this calculation and the calculated CFM to the appropriate Table 46, p. 95 through Table 49, p. 4.
- Page 96 Startup Table 48. 40 - 50 Ton Downflow Unit Economizer (O/A) Damper Static Pressure Setup Return Air Duct Static + Return Air Damper Static System Design (Inches of Water) 0.20 0.40 0.60 0.80 1.00 1.20 1.40 Drive Rod Position 12000 12500 13000 13500...
Page 97: Manual Fresh Air Damper
Page 98: starting the compressor, page 99: starting 40 to 50 ton units.
- Page 100 Startup Figure 53. Line Weight Locations—50 Ton Figure 54. Line Weight Locations—40 Ton RT-SVX34C-EN...
Page 101: Compressor Oil
- Page 102 Startup Table 52. 30 Ton—Operating Pressure (60 Hz) TC, TE, YC* 36 0 FULL LOAD 7 00 6 50 6 00 5 50 115 F OD Ambient 5 00 105 F OD Ambient 4 50 95 F OD Ambient 4 00 85 F OD Ambient 3 50 75 F OD Ambient...
- Page 103 Startup Table 54. 40 Ton Dual Circuit—Operating Pressure (60 Hz) TC, TE , YC* 4 80 Circuit # 1 Full Load 7 00 6 50 6 00 5 50 115 F OD Ambient 5 00 105 F OD Ambient 4 50 95 F OD Ambient 4 00 85 F OD Ambient...
- Page 104 Startup Table 56. 50 Ton Dual Circuit—Operating Pressures (60 Hz) TC, TE, Y C* 600 Circ uit # 1 FULL LO AD 115 F OD Ambient 105 F OD Ambient 95 F OD Ambient 85 F OD Ambient 75 F OD Ambient 65 F OD Ambient 55 F OD Ambient 11 0...
- Page 105 Startup Table 58. 22.9 Ton—Operating Pressure (50 Hz) TC, TE, YC* 27 5 FULL LOAD 7 00 6 50 6 00 5 50 115 F OD Ambient 5 00 105 F OD Ambient 4 50 95 F OD Ambient 4 00 85 F OD Ambient 3 50 75 F OD Ambient...
- Page 106 Startup Table 60. 29.2 Ton—Operating Pressures (50 Hz) TC, TE, YC* 35 0 FULL LOAD 7 00 6 50 6 00 5 50 115 F OD Ambient 5 00 105 F OD Ambient 4 50 95 F OD Ambient 4 00 85 F OD Ambient 3 50 75 F OD Ambient...
- Page 107 Startup Table 62. 33.3 Ton Dual Circuit—Operating Pressure (50 Hz) TC, TE , YC* 4 00 Circuit # 2 Full Load 4 200 3 700 46.1 F OD Ambient 40.6 F OD Ambient 3 200 35.0 F OD Ambient 2 700 29.4 F OD Ambient 23.9 F OD Ambient 2 200...
Page 108: Scroll Compressor Operational Noises
Page 109: charging by subcooling, page 110: electric heat units, page 111: final unit checkout, page 112: sequence of operation, page 113: units without an economizer, page 114: economizer operation based on reference enthalpy, page 115: gas heat sequence of operation, page 116: electric heat sequence of operation, page 117: low pressure control (lpc) sequence of operation (reliatel control), page 118: maintenance.
- Page 119 Maintenance Table 65. Supply Fan Sheave and Belt Table (a)(b)(c) )(d) )(e) Fan Sheave Fan Bushing Motor Sheave Motor Bushing Tons Motor RPM Browning Browning Browning Browning Belt BX108 BK190 X 1 7/16 BK190-1-7/16 BK62H BK62H H 1-3/8 H-1-3/8 Notched BX100 BK160 X 1 7/16 BK160-1-7/16 BK57H...
Page 120: Monthly Maintenance
- Page 121 Maintenance Table 67. Deflection Force Deflection Force (Lbs.) Belts Super Gripbelts Gripnotch Steel Cable Gripbelts Cross Small P.D Section Range Min. Max. Min. Max. Min. Max. 3.0 -3.6 4 1/2 3 7/8 5 1/2 3 1/4 3.8 - 4.8 3 1/2 4 1/2 6 1/4 3 3/4...
Page 122: Heating Season
Page 123: coil cleaning, page 124: fall restraint, page 125: refrigeration system, page 126: compressor replacements.
- Page 127 Maintenance Table 70. Compressor Models/Restrictor Locations Restrictor Location Model Compressor Compressor Compressor T**/Y** CPR3 CPR2 CPR1 CPR3 CPR2 CPR1 CSHD142 CSHD161 CSHD161 CSHD184 CSHD155 CSHD183 CSHD161 Figure 60. Compressors Table 71. Sample Operator’s Maintenance Log (see note) Refrigerant Circuit #1 Refrigerant Circuit #2 Current Ambien...
Page 128: Diagnostics
Page 129: terminal locations, page 130: diagnostics (cv units only), page 131: diagnostics (vav only), page 132: zone temperature sensor (zsm) service indicator, page 133: test 1, page 134: test 4.
- Page 135 Diagnostics Table 75. Constant Volume Defaults Component or Function Default Operation Cooling Setpoint (CSP) 74° F Heating Setpoint (HSP) Economizer 71° F Normal Operation Economizer Minimum Position Normal Operation Mode Normal operation, or auto if ZSM mode switch has failed Normal operation, or continuous if fan mode switch on ZSM has failed Night Setback Mode Disabled - Used with Integrated Comfort™...
Page 136: Test 1
Page 137: test 2, page 138: compressor-blink codes.
- Page 139 Diagnostics Table 77. Troubleshooting SYMPTOM PROBABLE CAUSE RECOMMENDED ACTION 1. No power to the Unit. 1. Check line voltage at service disconnect. 2. No power to the RTRM. 2. Check for 24 VAC at RTRM J1-1 to system ground. 3. Zone Sensor Module (ZSM) is 3.
- Page 140 Diagnostics Table 77. Troubleshooting (continued) SYMPTOM PROBABLE CAUSE RECOMMENDED ACTION 1. No power to CC1 coil. Possible 1. Check wiring, terminals and applicable controls Cool Failure (CCB1, HPC1, TDL1, WTL1, LPC1) 2. CC1 coil defective. Cool Failure 2. Check CC1 coil. If open or shorted, replace CC1. Indicated.
- Page 141 Diagnostics Table 77. Troubleshooting (continued) SYMPTOM PROBABLE CAUSE RECOMMENDED ACTION 1. CFM has failed. 1. Check CFM, replace if necessary. 2. Disconnect BROWN wires from capacitor, test, and 2. CFM capacitor has failed. replace if necessary. 3. Check wiring, and terminals. Repair, or replace if J.
- Page 142 Diagnostics Table 77. Troubleshooting (continued) SYMPTOM PROBABLE CAUSE RECOMMENDED ACTION 1. Check for 24 VAC at AH, BH,CH, and DH contactor 1. Heater contactor(s) have coils. If 24 VAC is present on a call for heat, and the failed. contacts do not close, the contactor has failed. 2.
- Page 143 Diagnostics Table 77. Troubleshooting (continued) SYMPTOM PROBABLE CAUSE RECOMMENDED ACTION 1. Check the return air sensor (RAS) at connector P10 by disconnecting P10 from RAT on the ECA. Check for resistance between P10-1 and P10-2, refer to the 1. Comparative enthalpy setup, Resistance versus Temperature Chart.
- Page 144 Diagnostics Table 78. Component Failure Mode COMPONENT FAILURE RESPONSE NORMAL RANGE DIAGNOSTIC 4 to 20 mA Check at ECA ECA 3 flashes. (RHS) Return Humidity 1. Economizer operates using 10 to 90% RH Honeywell RAH-1 and RAH-2 by Sensor Referance Enthalpy. C7600A.
- Page 145 Diagnostics Table 78. Component Failure Mode COMPONENT FAILURE RESPONSE NORMAL RANGE DIAGNOSTIC This input is for "indication only "Normal operation = 0 VAC SERVICE LED ON 2-30 VDC (CFS) Clogged Filter and does not effect the normal measured between terminals present at RTRM J6-6 and J6- Switch operation of the unit.
Page 146: Tr-1 And Tr-200 Vfd Programming Parameters
- Page 147 Diagnostics g. Press [OK] ►◄ h. To move to a different digit within a parameter setting, use the [ ] buttons (Highlighted area indicates digit selected for change) ▲ ▼ i. Use [ ] and [ ] buttons to adjust the digit j.
Page 148: Unit Wiring Diagram Numbers
- Page 149 Unit Wiring Diagram Numbers Table 81. Unit Wiring Diagram Numbers Diagram No. Descriptions 2313-0654 Control Box Connection Print - 27.5-35T, VAV, 36KW-54KW Electric Heat 208-230V 2313-0655 Control Box Connection Print - 27.5-35T, VAV, 36KW-54KW Electric Heat 380-575V 2313-0656 Control Box Connection Print - 40T, VAV, 54KW Electric Heat 208-230V 2313-0657 Control Box Connection Print - 40T, VAV, 54KW Electric Heat 380-575V 2313-0658...
Page 150: Warranty And Liability Clause
- Page 152 HVAC systems, comprehensive building services, and parts. For more information, visit www.Trane.com. Trane has a policy of continuous product and product data improvement and reserves the right to change design and specifications without notice. Produced with paper that uses fewer trees ©...
This manual is also suitable for:
Rename the bookmark, delete bookmark, delete from my manuals, upload manual.
- Knowledgebase
- Ask a Question
- Pinned -->
- Mark Forums Read
- Who's Online
- Thanks / Like Statistics
- Hottest Threads / Posts
- Contracting Business
- Advanced Search

- The ARPA Zone/Open Membership Discussion Forums
- Tech to Tech Chat - Commercial
Trane Voyager ignition control module
- Cookie Consent We use cookies to improve your website experience. To learn about our use of cookies and how you can manage your cookie settings, please see our Cookie Policy . By continuing to use the website, you consent to our use of cookies.
- Gain access to our free AOP (Ask a Professional) Section to get real answers for your questions. All this and much more is available to you absolutely free when you register ; for an account, so join our community today today! We suggest not registering using an AT&T, BellSouth, AOL or Yahoo email address. If you have any problems with the registration process or your account login, please contact support .
Thread: Trane Voyager ignition control module
Thread tools.
- Show Printable Version
- View Profile
- View Forum Posts
- View Forum Threads

md# YCD150D4LBBB ICM board #X13650882-01 Anyone have any detailed troubleshooting info. on this control? IO&M doesn't say much about it. Thanks!!

Originally Posted by chill67 md# YCD150D4LBBB ICM board #X13650882-01 Anyone have any detailed troubleshooting info. on this control? IO&M doesn't say much about it. Thanks!! All diagnoses and test are on the frnot of that small panel. That's it buddy. This POS does not tell you what failed. It just says "cool fail" or "heat fail" by measuring voltage between terminal 6,7,8. Even those blooming idiots from trane could not tell what part caused the failure. They say "cycle the power and hope for the best"

Will check Trane voyager manual and let you know if i find anything that helps!!!
- Visit Homepage

here you go
Last edited by dandyme; 01-07-2011 at 07:16 PM .
It`s better to be silent and thought the fool; than speak and remove all doubt.
Thanks for the info!!!

I guess the info was removed? Having a hard time finding this paperwork or PDF!
nothing in that profile indicates you are a service tech, more than likely, I removed it after giving them enough time to see it generally will not put tech lit in open forum, never know who's lurking out there
good luck ..... worst ignition system in the trade by far.....
it was working.... played with it.... now its broke.... whats the going hourly rate for HVAC repair

Moved to tech to tech commercial

Do you still have the info on the voyager,buddy?

I too would love some info on this board. Apparently it offers several configurations for wiring and operation, but info is very scarce.
Pro members should seek Pro info in the Pro forum.
[Avatar photo from a Florida training accident. Everyone walked away.] 2 Tim 3:16-17 RSES CMS, HVAC Electrical Specialist Member, IAEI AOP Forum Rules: Rules For Equipment Owners. Equipment Owners Find a Contractor HERE! Rules For Professional Members * To get your (*), Click Here. How to become a Professional Member.
- Private Messages
- Subscriptions
- Search Forums
- Forums Home
- The #1 question asked by NEW MEMBERS. Please read this...
- Questions About Becoming A Professional Member? Step Inside...
- SITE Software Issues? Post Them Here
- RULES for AOP - Owner Assistance and Contractors
- AOP Residential HVAC (Beenthere Zone)
- AOP Commercial HVAC
- General Discussion
- Job Wanted/Needed Discussion
- Industry and Forum News
- Webinars and Virtual Events
- Tech to Tech Chat - Residential
- Refrigeration & Ice Making
- Members Inventions **NEW
- Test & Balancing Forum NEW
- Control Sales Forum
- Professional Controls Forum
- Control Jobs Forum
- Chillers Open Forum
- Energy Efficiency and Building Performance Discussion NEW
- Commercial Food Service Equipment
- Residential Geo Thermal / Water Source
- Commercial Geo Thermal / Water Source
- Indoor Air Quality
- Tools & Test Equipment
- Food and Grill Forum
- "Wall of Pride" - Pictures
- "Wall of Shame" - Pictures
- How To Become a Pro and Rules For Pro Members
- Pro's Forum: General Discussion
- Charlie's Corner (Icemeister)
- HVAC Basics **NEW
- Pro Forum: Refrigerants and EPA regulations **NEW
- Pro's Forum: Business & Marketing
- Pro Forum: Residential Refrigeration and Appliances **NEW
- Pro's Forum: Sales
- Pro Forum: Equipment Recalls and Bulletins **NEW
- Pro's Forum: Residential
- Pro's Forum: Commercial
- Pro's Forum: Geo Thermal / Water Source
- Pro's Forum: Refrigeration & Ice
- Pro's Forum: Chillers
- Pro's Forum: Oil Burners
- Pro's Forum: Hydronics/Boilers
- Pro's Forum: Building Science Discussions
- Pro's Forum: Training and Education
- Pro's Forum: Instructors Forum NEW
- Pro's Forum: Tips 'n Tricks of the Trade
- Pro's Forum:The Gun Enthusiast
- Frequently Asked Questions About Submissions
- Manufacturers' Technical Information
- Articles Authored by Others
- Self-Authored Articles
- Submit Quiz Questions
- About the Suggestion Box
- Voice Your Opinions
- Share Ideas
- Report Problems
- Educational, Training & Reference Information
- Manufacturer's Technical Information Links
- Quiz Questions
- Open Forum Discussion
- Split Systems, Package Units, Furnaces
- Geothermal / Water Source Heat Pumps
- Specialty Systems
- Boilers Hydronic, Steam
- Accessories Humidifiers, Air Cleaners, HRUs, Fans, Filters, etc
- Components Coils, Heaters, Motors, etc.
- Compressors
- Oil Burners
- Systems - General
- Accessories Pumps, Cooling Towers, Evap Condensers, etc
- Components Valves, Motors, Condensers, Evaporators, etc
- Refrigeration Systems
- Evaporators, Condensers, Etc.
- Valves, Regulators, Filters, Etc.
- Walk-Ins, Cold Storage
- Food Service Equipment, Display Cases
- Supermarket Cases & Compressor Systems
- Ice Machines
- Controls, Motors, Etc
- HVAC Load Calc Software
- Refrigeration Load Calc Software
- HVACR Software & Online Training
- HVACR Calculators & Apps
- Formulas and Calculations
- In Memoriam
- Licensing, Laws, Codes and Certification
- Jokes, Quotations, Humor, Wisdom Pills
- Practice, Testing Area
- Plumbing Forum Rules
- Plumbing General Open Forum
- Pro's Forum: Plumbing Discussion
- Electrical Forum Rules
- Open Discussion Electrical
- Photovoltaic
- New Products
- Bonding & Grounding
- Motors & Motor Controls
- Test & Measurement
- Tools & Equipment
- Code Violations
- Pro's Forum: Power Quality
- Pro's Forum: Calculations & Electrical Theory
- Pro's Forum: Electrical Business & Marketing
- Pro's Forum: Estimating
- Job Postings
vBulletin Message
The following errors occurred with your submission, quick reply, register now.
Please enter the name by which you would like to log-in and be known on this site.
- Confirm Password:
Please enter a password for your user account. Note that passwords are case-sensitive.
- Email Address:
Please enter a valid email address for yourself.
- HVAC/R Contractor
- HVAC/R Technician/Installer
- HVAC/R Wholesaler/Distributor
- HVAC/R Manufacturer
- Manufacturer Rep
- HVAC/R Consultant
- HVAC/R Engineer
- Facilities manager/Mechanical Engineer
- Homeowner or Building/Equipment Owner (We welcome homeowners and Building owners. Help us customize your experience) Please post in the AOP Section
- Residential HVAC
- Light Commercial HVAC (up to 25 tons)
- Commercial HVAC (over 25 tons)
- Refrigeration
- Hydronic Heating
- Building Automation/Controls
Posting Permissions
- You may post new threads
- You may post replies
- You may not post attachments
- You may not edit your posts
- BB code is On
- Smilies are On
- [IMG] code is On
- [VIDEO] code is On
- HTML code is Off
Forum Rules
- HVAC-Talk.com
© VerticalScope Inc. All Rights Reserved.
Smart AC Solutions
Talked About Air Conditioners
Trane Defrost Control Board LED Codes | Solve Common Issue!
If your Trane furnace is equipped with a defrost control board , you can use the LED codes to help troubleshoot any problems that may arise. The most common code is the “red flash” which indicates that the board is in defrost mode.
Other codes include the “green flash” which means that the furnace is operating normally, and the “amber flash” which indicates a problem with the igniter.
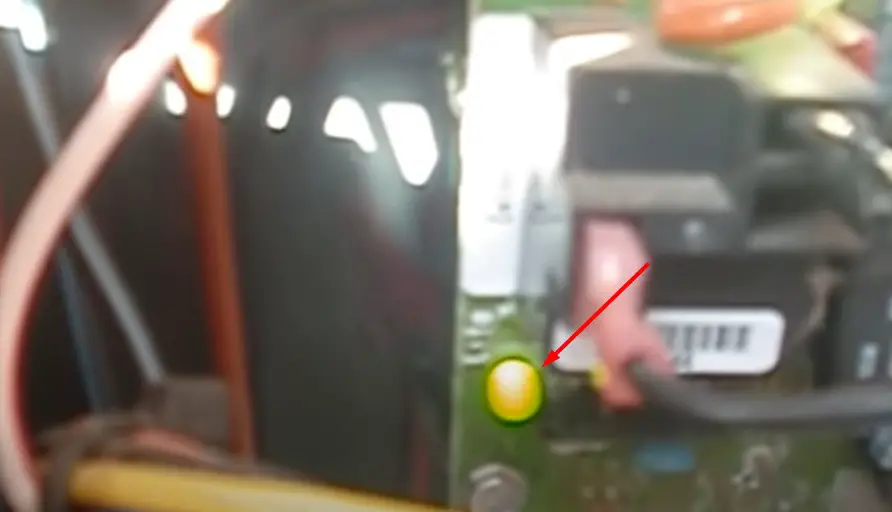
Page Contents
Trane Defrost Control Board LED Codes
The Trane Defrost Control Board is a crucial component of HVAC systems that helps to regulate the defrost cycle, ensuring the efficient functioning of the system. The board is equipped with LED codes that allow troubleshooting and identification of issues that could arise during operation.
The codes and their meanings are as follows:
- Steady Green LED – The system is operating normally.
- Steady Red LED – The defrost control board has detected a fault and is in lockout mode.
- Flashing Red LED – The sensor is not detecting proper temperature, indicating a possible faulty sensor or a wiring issue.
- Flashing Green LED – The system is in defrost mode, and the board is actively monitoring the process.
- Steady On – Power is present
- Flashing Slowly – Normal operation
- Flashing Rapidly – Defrost is active
- Two Flashes – High-pressure switch open
- Three Flashes – Low-pressure switch open
- Four Flashes – Auxiliary limit switch open
- Five Flashes – Outdoor temperature sensor fault
- Six Flashes – Reversing valve fault
- Seven Flashes – Defrost control board fault
Understanding these LED codes is crucial for HVAC technicians to identify and resolve any issues that may arise in the Trane Defrost Control Board.
What are the Codes for a Trane Furnace?
There is no one-size-fits-all answer to this question, as the codes for a Trane furnace will vary depending on the model and year of your furnace. However, you can generally find the code information for your furnace in the owner’s manual or by contacting Trane customer service.
How Do You Test a Trane Defrost Board?
There are a few things that you need to do in order to test a Trane defrost board. The first thing that you will need to do is locate the board. Once you have found the board, you will want to remove it from the unit. Next, you will want to check for any visual damage on the board. If there is any damage, you will want to replace the board. If there is no visual damage, you will then want to connect a multimeter to the board. You will want to set the multimeter to ohms and check for continuity between the two terminals on the board. If there is continuity, then the board is good. However, if there is no continuity, then the board needs to be replaced.
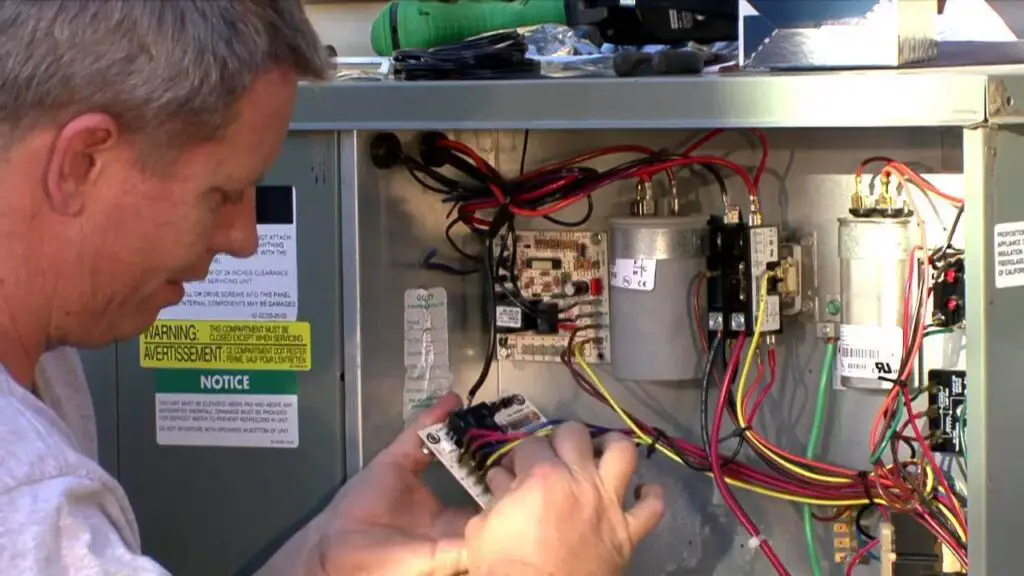
What Causes a Hard Lockout on a Heat Pump?
A hard lockout on a heat pump is caused by a number of different things. The most common cause is when the outdoor temperature drops below the minimum set point for the heat pump. This can be caused by a number of different things, including a cold front moving in, or simply the temperature dropping at night. When this happens, the heat pump will shut off completely in order to prevent damage from happening to the unit. Another common cause of a hard lockout is when the indoor temperature sensor fails. This can cause the heat pump to think that the indoor temperature is too low, even when it isn’t, and as a result, it will shut off. Finally, if there is a problem with the outdoor fan, this can also cause a hard lockout. If the fan isn’t able to turn on, then the heat pump won’t be able to circulate air properly and it will shut down in order to prevent overheating.
What Does Hard Lockout Mean on a Trane Heat Pump?
If your Trane heat pump is locked out, it means that the system has been turned off and can’t be restarted until a qualified technician resets it. This usually happens when the system detects a problem that could cause damage or harm, such as an overheating condition.
Once the problem has been resolved, the lockout can be reset and the heat pump will operate normally again.
Trane 4Twr4 Fault Codes
If you’re a Trane 4TWR4 owner, you know that these units are some of the most reliable and durable on the market. But even the best units can develop faults over time. If your 4TWR4 is displaying a fault code, it’s important to know what that code means so you can take steps to fix the problem. There are four main fault codes that your 4TWR4 may display:
• Code 01: This indicates that there is a problem with the unit’s condenser fan. The most likely cause is a dirty or damaged fan blade. You’ll need to clean or replace the blade to fix this problem.
• Code 02: This indicates that there is a problem with the unit’s evaporator fan. The most likely cause is a dirty or damaged fan blade. You’ll need to clean or replace the blade to fix this problem.
• Code 03: This indicates that there is a problem with the unit’s compressor. The most likely cause is a blown fuse or tripped breaker.
Trane LED Codes
If you have a Trane furnace, you may be wondering what the different LED codes mean. Here is a list of the most common codes and their meanings:
Blinking Green Light: This indicates that the furnace is in standby mode and waiting for a call for heat. Solid Green Light: This means that the furnace is operating normally.
Flashing Red Light : This code indicates that there is an error with the furnace. The specific error will be displayed on the control panel. Consult your owner’s manual for troubleshooting steps.
Continuous Red Light: This means that the limit switch has been activated and the furnace needs to be serviced by a qualified technician.
Trane Furnace Error Codes
Trane furnace error codes are an essential diagnostic tool for identifying issues with your heating system. These codes not only help technicians identify problems quickly but also provide homeowners with the necessary information to troubleshoot issues before calling a professional.
Here are the most common Trane furnace error codes and their meanings:
- 2 flashes: Indicates a problem with the pressure switch.
- 3 flashes: Indicates an issue with the draft inducer motor.
- 4 flashes: Indicates an open limit switch.
- 5 flashes: Indicates a problem with the flame sensor.
- 6 flashes: Indicates an issue with the rollout switch.
- 7 flashes: Indicates a problem with the gas valve.
- 8 flashes: Indicates a problem with Low flame sense signal.
- 9 flashes: Indicates a problem with Igniter.
By familiarizing yourself with these codes, you’ll be better equipped to handle any furnace issues that arise.
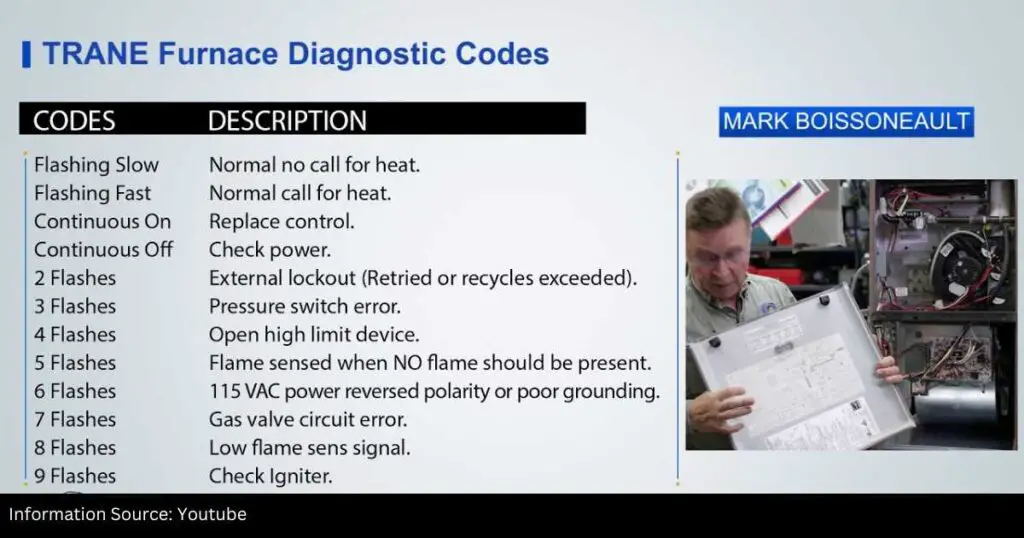
Besides the above, you may also find the following error codes for Trane Furnace:
- 126: Internal control fault
- 131: Ignition failure
- 132: Flame sensor failure
- 133: Limit circuit fault
- 147: Low flame signal
- 151: Blower motor fault
- 161: AC power loss
- 164: Open high-limit device
These error codes can help a technician quickly identify the issue and provide a solution, ensuring that your Trane furnace runs smoothly and efficiently.
Trane Troubleshooting Guide
If your Trane unit isn’t working properly, you may be able to troubleshoot and fix the problem yourself. This Trane Troubleshooting Guide will help you identify common issues and provide solutions. First, check the thermostat to make sure it is set correctly. If the thermostat is set too low, the unit won’t run. If the thermostat is set too high, the unit will run continuously without cooling the home. Next, check for power failures. The circuit breaker may have tripped or a fuse may have blown. Reset the breaker or replace the fuse and see if that fixes the problem. If your unit still isn’t running, there could be an issue with the actual unit itself. First, check to see if there is debris blocking the air intake or exhaust vents. If so, remove the debris and try again. Next, check for freezing coils. Ice can build up on the coils and prevent proper airflow. Turn off your unit and let it thaw for several hours before restarting it again. Finally, if all else fails, call a professional for assistance.
Trane Air Handler Blinking Lights
If you have a Trane air handler in your home, you may have noticed that the lights on the unit are blinking. While this may be alarming at first, it’s actually a normal part of the unit’s operation. The blinking lights indicate that the air handler is in standby mode and is waiting for a command from the thermostat. Once the thermostat tells the air handler to start, the lights will stop blinking and the unit will begin heating or cooling your home as needed.
Trane Voyager Error Codes
If you’re getting error codes on your Trane Voyager, it means there’s a problem with the unit. Here are some common error codes and what they mean:
E01 – This indicates that the evaporator temperature is too high. Check to make sure that the coils are clean and that the air filter isn’t clogged.
E02 – This code means that the condenser temperature is too high. Again, check the coils and air filter. Make sure the unit has proper ventilation.
E03 – The third code stands for “freeze protection.” This means that the unit is sensing a potential for freezing temperatures and is shutting down to prevent damage. Check your thermostat settings and make sure the unit is in heating mode. If it still doesn’t work, call a technician. These are just a few of the most common Trane Voyager error codes . If you’re experiencing problems with your unit, don’t hesitate to call a technician or reference your owner’s manual for more information.
Trane Ac Blinking Green Light
If you have a Trane air conditioner , you may have noticed that the green light is blinking. This is normal and indicates that the unit is in standby mode. The green light will blink when the unit is first turned on, and then it will remain lit when the unit is running. If the green light starts blinking again, it means that the unit has been turned off and is in standby mode once again.
Trane Eev Control Board Troubleshooting
If you have a Trane EEV control board that is giving you trouble, there are some things you can do to troubleshoot the problem. First, check all of the connections to make sure they are tight and secure. Next, check the circuit breaker to see if it has tripped. If neither of these solutions solves the problem, you may need to replace the control board.
Heat Pump Defrost Board: Diagnostic Procedures
The Trane Defrost Control Board is responsible for managing the defrost cycle of your Trane AC unit. If there is a problem with the board, it will display an error code on the LED display.
This article lists the codes and what they mean, so you can troubleshoot the issue and get your AC unit up and running again.
Related Articles:
- Mitsubishi Msz-Fh12Na Troubleshooting | Solve Common Issues
- Carrier APU AC Not Working: Identify and Fix the Issue!
- P6 Error Code on Your Air Conditioner
- Trane Ac Unit Fan Not Spinning
My name is Aris, and I am a certified HVAC technician. I have been working in this field for over 5 years and have a lot of experience with different AC units. I write here to help people solve their Air Conditioning problems and find the best solutions for their needs.
If you are having any issues with your air conditioner or are thinking about buying a new one, be sure to check out my blog!
Leave a Reply Cancel reply
Your email address will not be published. Required fields are marked *
Save my name, email, and website in this browser for the next time I comment.

IMAGES
VIDEO
COMMENTS
List of Light Commercial LED Codes. LED Blink Codes. Electromechanical Ignition Board. 2 flash - 1 Hour Lockout. 3 flash - Pressure Switch. 4 flash - TCO Open. 5 flash - Flame W/O Gas. 6 flash - Rollout Switch Open. 7 flash - W1 / W2 Swapped.
Ignition Controller Board Module Diagnostics. Symbio 700 Ignition Diagnostics LED 1. Pressure switch problem detected. (no vent air flow, bad CBM, closed at an initial call for heat). Auto reset. High Limit switch protection device open (excessive heat in combustion chamber, low airflow). Auto reset. Flame sensed and gas valve not energized, or ...
Voyager ™ Commercial ... 600B (60 Hz/3 phase) 50 Hz/3 phase: TC*, TE*, YC*275B, 305B, 350B, 400B, 500B ©2021 Trane RT-SVX34U-EN Introduction Read this manual thoroughly before operating or servicing this unit. Warnings, Cautions, and Notices ... Failure to follow code could result in death or serious injury. All field wiring MUST be ...
Wiring issue or problem with ignition module or RTRM. 2 Flash. System lockout - failure to sense flame. Failure to ignite, no spark, low/no gas pressure. 4 Flash. TCO (high temperature limit) circuit open. excessive heat in the combustion chamber, low airflow, 5 Flash. Flame being sensed, but gas valve not energized.
Voyager™ 3 Packaged Rooftop Air Conditioners with Symbio™ ... TE*, YC*, 275C, 305C, 350C, 400C, 500C ©2023 Trane RT-SVX34W-EN Introduction Read this manual thoroughly before operating or servicing this unit. Warnings, Cautions, and Notices Safety advisories appear throughout this manual as ... Failure to follow code could result in death ...
Light Commercial Power Burner troubleshooting Guide. Light Commercial Power Burner Troubleshooting Guide. Overview: This Guide directs customers to gas pressures setup, ignition board codes and troubleshooting. To obtain a hard copy of this Guide please contact your local Trane Parts Center. WARNING:
into a sealed drum where ignition takes place. It is more reliable to operate and maintain than a multiple burner system. † The hot surface ignitor is a gas ignition device which doubles as a safety device utilizing a continuous test to prove the fl ame. Weather Tight Top and C abinet † Voyager units incorporate the Trane-Tite-Top (T 3). Each
Summary of Contents for Trane Voyager Commercial. Page 1 Installation, Operation, and Maintenance Voyager™ ™ Commercial Packaged Rooftop Air Conditioners with ReliaTel™ Controls and eStage™ 27.5 to 50 Tons - 60 Hz 22.9 to 41.7 Tons (81-148 kW) - 50 Hz "B" and later design sequence 6 6 0 0 H H z z / / 3 3 p p h h a a s s e e : TC ...
Easy Access Low Voltage Terminal Board Voyager's Low Voltage Terminal Board is external to the electrical control cabinet. It is extremely easy to locate and attach the thermostat wire. This is another cost and time saving installation feature. Indoor Air Quality • Filters. All rooftops are shipped with throw-away
Summary of Contents for Trane Voyager Commercial. Page 1 Installation, Operation, Maintenance Voyager™ Commercial 27.5 to 50 Ton 60 Hz 22.9 to 41.7 Ton 50 Hz CV or VAV Rooftop Air Conditioners with ReliaTel™ Controls, R-410A Refrigerant Model Numbers "B" and later design sequence TC*, TE*, YC*330B, 360B, 420B, 480B, 600B (60 Hz/3 phase ...
YSC - Ignition Fault Codes. Article ID: 494. Last updated: 13 Nov, 2020. Trane Package Unit: YSC. Re: Ignition Lockout Codes. Trane YSC package units are multi-stage gas/electric units. These units utilize an Ignition Control Board (ICB) with a built-in spark generator for electronic ignition control. The ICB has a diagnostic light to indicate ...
Packaged Rooftop Air Conditioners Voyager™Commercial with ReliaTel™Controls. Including eStage™ 27.5 to 50 Tons - 60 Hz 22.9 to 41.7 Tons (81-148 kW) - 50 Hz. ©2021 TraneRT-PRC033N-EN. Introduction. Packaged Rooftop Air Conditioners. Through the years, Trane has designed and developed the most complete line of Packaged Rooftop products ...
Method 1. To reset the system from the space, turn the "Mode" selection switch at the thermostat to the "Off" position. After approximately 30 seconds, turn the "Mode" selection switch to the desired mode, ie...Heat, Cool, or Auto. Method 2. To reset the system at the unit, cycle the unit power by turning the disconnect switch "Off" and then "On".
Trane Voyager ignition control module. md# YCD150D4LBBB. ICM board #X13650882-01. Anyone have any detailed troubleshooting info. on this control? IO&M doesn't say much about it.
Learn how to service, diagnose and wire Trane branded Samsung units with this comprehensive manual. Download or access online.
12.5 through 25 ton YCD and YCH units with the first three digits of their serial numbers starting with 543 through 826, that previously had ReliaTel control board version 6.0 installed. Overview: If you replace RTRM version 6.0 with a newer version RTRM, check the Ignition Board J1 connector for a wire in Position 5 going to ground.
Ignition Board unresponsive after RTRM replacement; Voyager 2 Combustion Fan Power Wiring Info (with the CFR Relay) Voyager 2 Staged Gas Manifold Pressure; Voyager II - Negative Pressure Gas Valve Adjustment; Voyager Light Commercial Flue Product Analysis; What are the gas heat fault codes for Reliatel controlled Voyager II units?
The codes and their meanings are as follows: Steady Green LED - The system is operating normally. Steady Red LED - The defrost control board has detected a fault and is in lockout mode. Flashing Red LED - The sensor is not detecting proper temperature, indicating a possible faulty sensor or a wiring issue. Flashing Green LED - The ...
Troubleshooting Tips: The flame rod circuit is energized (with 110 vac) anytime the board is powered up.; The voltage on the flame rod circuit drops to 90 vac on trial for ignition. There is no 24 vac on P1-9 (powering the Rollout Switch, Pressure Switch and TCO1 & TCO2) until there is a call for heat.; You can bypass the Pressure Switch (for troubleshooting purposes) by waiting until the ...
Trane believes that responsible refrigerant practices are important to the environment, our customers, and the air conditioning industry. All technicians who handle refrigerants must be certified.The Federal Clean Air Act (Section 608) sets forth the requirements for handling, reclaiming, recovering and recycling of certain
Follow. Overview: Possible Causes (1-22) 1. Supply fan fail. 2. Zone temperature sensor input failure on CV units. 3. Programmable ZSM communication failure.
Wiring issue or problem with ignition module or RTRM. 2 Flash. System lockout - failure to sense flame. Failure to ignite, no spark, low/no gas pressure. 4 Flash. TCO (high temperature limit) circuit open. excessive heat in the combustion chamber, low airflow, 5 Flash. Flame being sensed, but gas valve not energized.